溶接業界では、熟練した人材の不足が大きな課題となっている。TIGや MIGのような伝統的な溶接技術は、習得に長年の経験を必要とすることが多い。しかし、現代の進歩、特にハンドヘルド・レーザー溶接は、数年ではなく数週間で習得できるソリューションを提供している。ジョー・ダラロサが執筆したこの記事では、従来の溶接方法とレーザー溶接の基本的な違いを説明し、この最新技術が生産性と収益性をどのように向上させるかを溶接工が理解できるようにします。
溶接の最新オプション光子 vs 電子
従来の溶接プロセスの多くは、金属部品間の融合を達成するために電気、または電子を使用しています。これらのプロセスには、電子ビーム溶接(EB)、ガス・タングステン・アーク(TIG)、シールド・メタル・アーク(SMAW)、ガス・メタル・アーク(MIGまたはMAG)、原子状水素溶接、スポット溶接、プラズマ・アーク、カーボン・アーク、引き抜きアーク(スタッド溶接)などがあります。この記事では、光子によるレーザー溶接と電子によるレーザー溶接の基本的な違いについて説明します。
伝統的な溶接技術
従来の電子溶接では、交流または直流の電圧源が必 要であった。電圧源は、溶接する材料の厚さに必要な 電流を供給する。これらの電子は、タングステン・チップ(TIG)、 金属ワイヤー(MIG)、フラックス・コーティング・ロッド(SMAW) などの電極を経由して被溶接物に送られる。電流を流すためには、被加工物を電気アースに接続する必要がある。
電子溶接の原理は単純で、電気アークが電極とワークピースを橋渡しし、プラズマを発生させる電流(電子)の流れを生じさせる。このプラズマと電流の流れによって溶融した溶接池が生成され、アークが進む(進行する)につれて凝固し、2つの部品を接合する。
この溶融池の温度は2500°C (4530°F) に達する可能性があり、窒素、アルゴン、ヘリウムなどのシールド・ガスで酸化性雰囲気から保護する必要がある。最新の溶接機には、精密な電流制御、アークを発 生させ安定させる高周波変調、パルス・アーク 機能などが装備されており、高品質の溶接を容易に 実現できる。
従来の溶接における課題
直流電子溶接では磁場が発生するため、アークが乱 れ、被加工物まで最短距離で流れなくなる可能性が あることに留意すべきである。これは、飛散や気孔な ど、溶接ビードの不均一性の原因となる。交流の電流は交流であるため、磁場の発生に はほとんど影響しない。直流プロセスは、より制御性の高いアーク を発生させるため、一般に溶接工に好まれ、その結果、飛 びはねが少なく、溶接ビードの外観も良くなる。
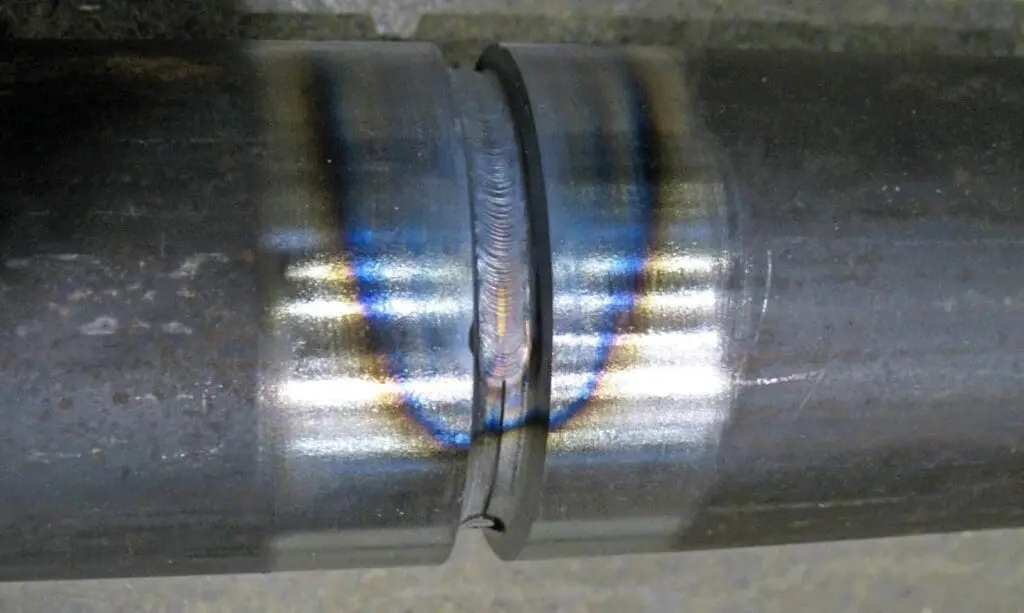
従来の溶接プロセスでは、大きな熱影響部(HAZ) が発生し、周囲の材料の特性に変化が生じる。このため、特性の異なる複数の領域が生じ、溶接の品質と強度に影響を及ぼす可能性がある。
レーザー溶接

レーザー溶接は、従来の方法に代わる現代的な方法であり、正確で効率的な結果をもたらします。最初の実用的なレーザーは、1960年にセオドア・マイマンによって実現されました。わずか60年余りの間に、レーザーは現代のインフラに不可欠なものとなりました。この記事を読んでいるあなたは、今まさにレーザーを直接または間接的に使用している可能性が高い。レーザーの使用には、波長(色)、出力、レーザースポットの大きさ、連続波(CW)またはパルスモードでレーザーを使用し、繰り返し周波数とパルス幅(特定のサイクル中に光が点灯している時間)を変えるなど、いくつかの異なる光の特性が含まれます。
レーザー溶接には光子源が必要で、この光源はレーザー・ダイオードによって直接被加工物に照射されるか、または、用途に応じたレーザー光を生成する材料をドープしたファイバー(「ポンピング」と呼ばれる)にレーザー光を通すことによって照射される。 この光(光子)は次にガラス・ファイバーを通って伝送され、一連のレンズを通って材料に集光される。この光はスペクトルの赤外線部分にあり、生成されたレーザー光は効率的に生成され、一部の金属に吸収されることがある。虫眼鏡を使って太陽で火を起こすことを想像してみてください。
レーザー溶接の種類
熱伝導溶接
このプロセスでは、集光された光で表面近くの材料を加熱し、溶接プールを形成します。光子のエネルギーが熱伝導によって溶接部に入り、滑らかで美観に優れ、精密な溶接が行われる。
ディープ・ペネトレーション/キーホール溶接
このプロセスでは、集光された細いビームを使用して、溶融材料の深く狭い溝を作ります。 副産物として金属蒸気が放出され、数ミリ秒のうちに空洞が形成されます。この蒸気で満たされた空洞は キーホールと 呼ばれ、レーザーが進む(移動する)につれて溶融金属で満たされる。 このタイプの溶接では、厚さ1/2インチ以上の材料に使用できる狭い溶接チャンネルが形成される。
レーザー溶接の利点
レーザー溶接は、従来の電子溶接より最大10倍高速であることが実証されている。10MW/cm²(1.6MW/in²)に近い出力密度で小さな集光スポットを生成するため、熱影響部が小さくなります。このため、溶接部の強度、外観、完全性において明らかな利点がある。さらに、レーザー溶接は短期間で習得できるため、新しいスタッフが数年ではなく数週間で熟練できるようになり、業界の人材不足に対処できます。
結論
レーザー溶接は、従来の溶接方法と比較して、効率性、精度の向上、トレーニング時間の短縮など、数多くの利点を提供します。レーザー溶接に移行することで、企業は人材不足に対処し、生産性を向上させ、収益性を高めることができる。この分野で特に進歩しているのはハンドヘルド・レーザー溶接で、従来のレーザー溶接の精度と効率に加え、さまざまな作業環境で必要とされる柔軟性と使いやすさを兼ね備えています。Theo MA1レーザー溶接機のようなハンドヘルド・レーザー溶接機は、機動性と多用途性を必要とする作業に最適であり、現代の溶接ニーズにとって優れた選択肢となっている。
ニュースレターに登録して、溶接技術の最新情報を入手しましょう。最新情報、ヒント、専門家の見解を直接受信トレイにお届けします。登録はこちらから。