Laser welding is an advanced and highly productive technology, but it comes with unique safety challenges. Understanding the potential hazards of laser welding is crucial for creating a safe working environment. If you’re new to laser welding, it might seem overwhelming, but there’s no need to worry.
Keeping a welding environment safe with lasers is straightforward and cost-effective with the right knowledge and practices. Follow these best practices and use the right safety equipment to make laser welding as safe, as traditional methods.
Why a Safe Working Environment is Essential
Laser welding uses high-powered laser beams, which can be dangerous if not managed properly. Unlike conventional welding, laser welding uses concentrated beams of invisible infrared (IR) light. These beams can cause severe burns and eye damage. Additionally, like conventional welding, laser welding generates harmful fumes and UV light, posing specific safety concerns.
Setting Up a Safe Laser Welding Space
Step 1: Designate a Controlled Area as a Laser Welding Space
Start by designating a controlled area solely for laser welding. This minimizes unnecessary access and exposure to laser hazards. Ensure the area is clearly marked and restricted to authorized personnel only.
Step 2: Install Laser Welding Enclosures or use a Light-Tight Room
Laser welding enclosures are essential for containing laser light and preventing accidental exposure. These safety cabins absorb and contain the laser beams, keeping them within a controlled area. This is crucial because the high-powered beams can cause severe harm if they contact skin or eyes. Using an enclosure ensures that all laser activity is safely contained, protecting everyone nearby.
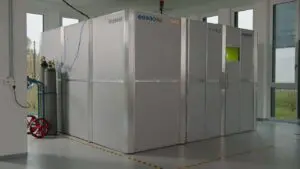
Alternatively, you can designate a light-tight room. This setup also prevents laser light from escaping the designated area, offering similar protection as enclosures. Proper containment of laser light is key to avoiding accidental exposure and maintaining a safe workspace.
Step 3: Use Laser Curtains and Barriers
Laser curtains offer a flexible solution for encapsulating the working area. These curtains block or absorb laser light and can be used as a replacement for a full enclosure or light-tight room. They are particularly useful when more mobility is needed in the work area, such as for mobile welding jobs. Laser curtains allow you to define the work area flexibly, adapting to different project needs. Additionally, they can be combined with enclosures or light-tight rooms to enhance safety, providing a versatile and effective way to contain laser light and protect everyone in the vicinity.
Step 4: Implement Room Interlock Systems
Room interlock systems are a crucial safety feature that enhance the security of your laser welding environment. These systems are designed to automatically shut off the laser if the door to the welding area is opened unexpectedly. Here’s how it works: when the door to the controlled area is closed, the interlock system completes a circuit, sending a signal to the laser welding machine which allows the laser to fire. However, if someone tries to enter and opens the door, the interlock system immediately detects this and cuts the power to the laser. This prevents accidental exposure to the laser beams and ensures that the laser only operates when the workspace is secure.
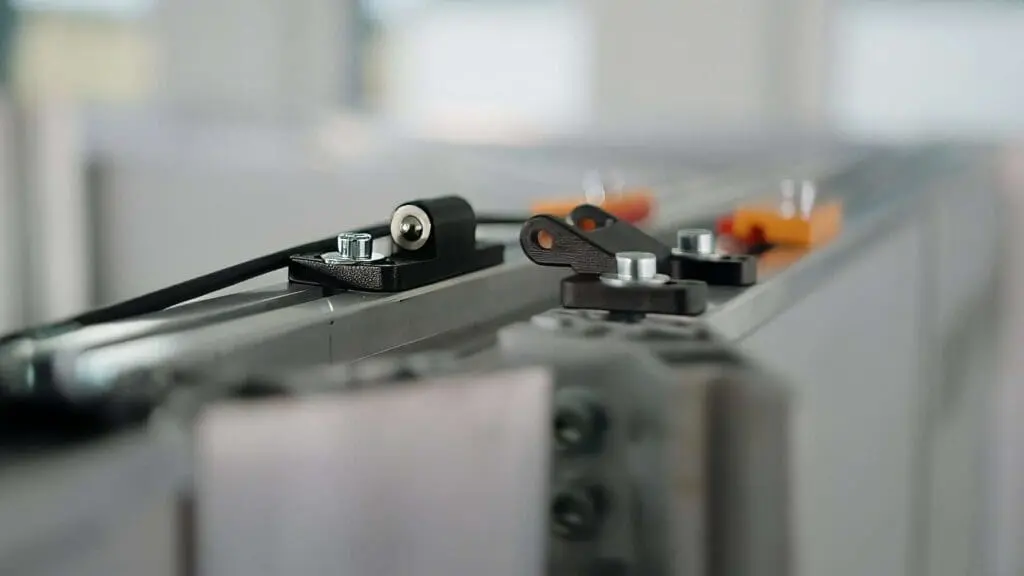
Additionally, there are curtain systems with interlock capabilities. These systems function similarly, where the laser is automatically shut off if the curtain is moved or opened unexpectedly. Implementing either door or curtain interlock systems significantly reduces the risk of accidental injuries and maintains a safe working environment for everyone in the area.
Step 5: Install Viewing Windows and Safety Glass
If your workspace includes windows or viewing panels, either completely block them with lightproof material such as sheet metal, or install safety glass that filters specific wavelengths of the laser. This protects anyone observing the welding process from harmful radiation. Safety windows with an Optical Density (OD) rating greater than 6 are recommended. Installing closed circuit cameras with monitors placed outside the laser welding area may be more cost effective than replacing with IR coated material, depending on the size of panel area to be blocked.
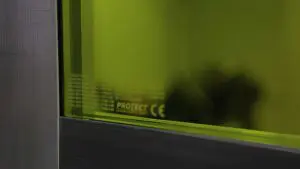
Step 6: Display Proper Warning Signs
Appropriate warning signs are crucial for maintaining safety in a laser welding environment. Display warning signs at all entry points, clearly indicating that a laser is in use. These signs must comply with safety standards and include information about the type and class of laser, potential hazards, and required personal protective equipment (PPE). An illuminated “Laser On” warning sign at each entrance, activated automatically when the laser emits light, is recommended. Regulations on proper warning signs vary by country and region, so consult local regulations or our Solution Partners for guidance.
Step 7: Ensure Fume Extraction and Air Quality Management
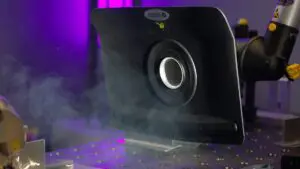
Maintaining air quality is essential in any welding environment. While laser welding produces a smaller Heat Affected Zone (HAZ) and less spatter [HS1] compared to traditional methods, it still generates fumes and particles that can be hazardous if inhaled. To protect your health, use an effective fume extraction system to remove these contaminants from the air, ensuring a safe breathing environment. Additionally, conduct regular air quality checks by licensed safety authorities to monitor and enhance the safety of your workspace. These measures are vital for maintaining a clean and safe environment for everyone involved in the welding process.
Step 8: Equip with Fire Protection Measures
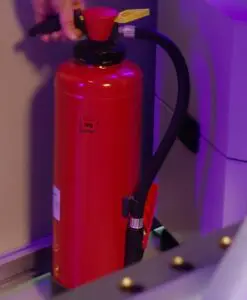
Best Practices for as safe Laser Welding Work Environment
By setting up your workspace with these essential safety measures, you create a secure environment for laser welding. Next, let’s look at the best practices that ensure ongoing safety and efficiency in your daily operations.
Proper Training and Awareness
Ensure all personnel are adequately trained in laser welding safety. Regular safety training sessions reinforce the importance of following safety protocols and staying informed about the latest safety measures.
Regular Maintenance and Inspections
Keeping on top of any required maintenance of laser welding equipment and safety systems ensures they function correctly. Regular inspections help identify potential issues before they become significant problems.
Personal Protective Equipment (PPE)
Using appropriate PPE is crucial. This includes wearing laser safety glasses with the correct OD rating, flame-resistant clothing, and suitable respiratory protection.
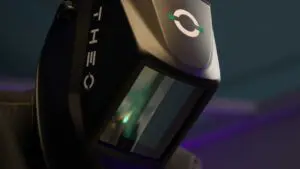
Safe Work Practices
Implement safe work practices, such as managing reflective and flammable materials, ensuring proper ventilation, and maintaining a clean workspace, to significantly reduce the risk of accidents and injuries.
Conclusion: Building a safe Laser Welding Work Environment.
Building a safe working environment for laser welding involves planning, appropriate safety measures, and a commitment to continual training and maintenance.
Working with THEO Solution Partners to build a safe Laser Welding Space
At THEO, we understand the importance of a safe working environment for laser welding. Our solution partners can assist you in finding the right safety solutions tailored to your specific needs. From high-quality enclosures and interlock systems to advanced fume extraction and fire protection measures, we provide comprehensive support to ensure your workspace meets the highest safety standards.
With proper safety measures in place, laser welding can be as safe as traditional techniques.
Join us at THEO Academy
For more in-depth training on laser welding safety, join our online courses at THEO Academy. Our courses are designed to equip you with the knowledge and skills needed to create a safe and efficient laser welding environment.
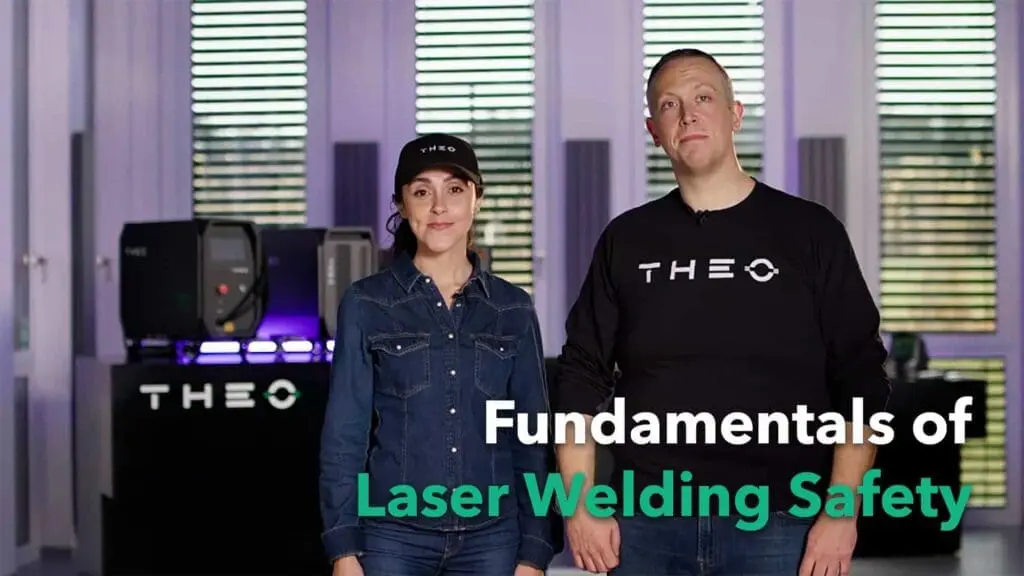